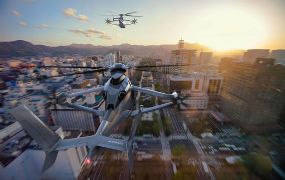
Hij is snel, licht en verbruikt weinig brandstof: de supersnelle RACER-helikopter kan vliegen met snelheden tot 400 kilometer per uur. De schaalcomponenten van de buitenhuid worden op een sterk geautomatiseerde manier vervaardigd met behulp van een nieuw type productieproces. Een onderzoeksteam van het Duitse Fraunhofer Institute for Foundry, Composites and Processing Technology IGCV ontwikkelde de innovatieve, duurzame methode samen met Airbus Helicopters.
Met meer dan 400 kilometer per uur is de Airbus Helicopters RACER, een afkorting voor Rapid and Cost-Effective Rotorcraft, veel sneller dan conventionele helikopters, die snelheden kunnen halen van ongeveer 230 tot 260 kilometer per uur. Maar dat is niet het enige speciale kenmerk dat de helikopter opvalt.
De bovenste lagen van de zijschalen zijn gemaakt van koolstofvezelversterkte kunststof (CFRP), de sandwichkern is gemaakt van fenolhars-honingraat. Tot nu toe werden dergelijke grote sandwich-achtige schalen met de hand vervaardigd met behulp van het handmatige legproces - een tijdrovend en kostbaar proces. Onderzoekers van Fraunhofer IGCV in Augsburg hebben in samenwerking met Airbus Helicopters een productieproces ontwikkeld waarmee de CFRP-schaalcomponenten op een sterk geautomatiseerde manier kunnen worden vervaardigd.
De ontwikkeling wordt gefinancierd als onderdeel van het EU CleanSky 2-programma. Het Fraunhofer Institute for Short-Term Dynamics, Ernst Mach Institute EMI in Freiburg, ondersteunt en coördineert de bemiddeling en communicatie tussen Brussel en de deelnemende Fraunhofer Institutes. Als een goed voorbeeld van Europese coördinatie en integratie brengt het demonstratieplatform meer dan 25 consortia in 13 landen uit de industrie en de wetenschap samen, ondersteund door een uitgebreid ecosysteem van kmo's - verenigd in het streven van de EU om een groenere luchtvaart te bereiken.
De automatisch vervaardigde schaalsegmenten van 3,4 x 1,5 meter vormen het achterste rechter- en linkerdeel van de kunststoffen buitenhuid van de Racer. Ze verbinden de staartboom met de romp. “Tot nu toe zijn de schalen ook gemaakt met koolstofvezelversterkte lichtgewicht materialen, maar we hebben het productieproces verder ontwikkeld. Het is nu gebaseerd op het zogenaamde Automated Fiber Placement Process”, zegt Thomas Zenker, wetenschapper bij Fraunhofer IGCV.
Een robot deponeert automatisch de continue vezelversterkte, voorgeïmpregneerde materialen. Er wordt gebruik gemaakt van unidirectionele tapes, die betere mechanische eigenschappen hebben en minder afval genereren dan op textiel gebaseerde kunststofcomposieten. De sandwichkern van fenolhars-honingraat draagt bij aan de stijfheid van het composiet, terwijl de vezels van de buitenlaag zorgen voor stevigheid.
“Voordat het materiaal uitgehard is, plaatst de robot de hoogwaardige vezels in een gereedschap. De robot volgt een speciaal ontwikkelde programmeer-methode. Het gereedschapsconcept is speciaal ontwikkeld voor de procesketen. Het oppervlak bepaalt de vorm die de vezels moeten aannemen wanneer ze automatisch worden afgezet. Er wordt rekening gehouden met de complexe geometrieën van de verschillend gevormde zandgewichtzakken. De tapes worden precies daar geplaatst waar de structuur van het latere onderdeel dit vereist”, vat de ingenieur het proces samen.
RACER heeft een groot duurzaamheidspotentieel
Afhankelijk van de gelaagdheid en vezels, bereikt een CFRP-component vervaardigd met behulp van Automated Fiber Placement een hoger draagvermogen dan een stalen element, terwijl het aanzienlijk minder weegt. "Dit is een belangrijk aspect in de luchtvaart, waar elke bespaarde kilo bijdraagt aan een lager brandstofverbruik", zegt de onderzoeker. Het bespaarde materiaal vermindert het gewicht van de schaalsegmenten met vijf procent.
Afhankelijk van de energiemix die bij de productie wordt gebruikt, kan de ecologische voetafdruk met maximaal 15 procent per schelpsegment worden verbeterd.
Geautomatiseerde vezelplaatsing voor afvalarme processen
Daarnaast heeft het doorontwikkelde productieproces nog meer voordelen: Zenker en zijn team zijn in staat om productieafval te verminderen van 45 naar 20 procent dankzij het efficiëntere proces. Afhankelijk van hoeveel helikopters er worden gemaakt, kan het automatische proces ook productiekosten besparen in vergelijking met conventionele handmatige productie. Bij een productie van bijvoorbeeld 65 helikopters per jaar is dat 20 procent.
In augustus 2020 zijn de twee zijdelen voor het prototype van de helikopter opgeleverd. Dit werd gevolgd door uitharding en niet-destructieve materiaal-testen bij Airbus, waarbij de componenten met behulp van een ultrasoon proces worden geröntgend op mogelijke defecten. Nieuwe combinaties van materiaal en productieproces vereisen intensieve herziening, vooral in veiligheidskritieke industrieën zoals de luchtvaart. In het kader van permit-to-flight-testen werden aanvullende karakteristieke waarden van materiaalmonsters bepaald en geëvalueerd. Deze mechanische tests zijn een voorwaarde om de Racer-demonstrator vrij te geven voor de vlucht.
De componenten van Fraunhofer IGCV hebben de test doorstaan en worden momenteel geassembleerd tot een prototype. Het is de bedoeling dat de 'duurzame' helikopter begin 2022 wordt opgeleverd en zijn eerste testvlucht maakt.
Zijn hoge snelheid maakt hem ideaal voor gebruik in allerlei noodsituaties. Het is echter ook denkbaar om hem als luchttaxi te gebruiken om passagiers tussen stedelijke centra te vervoeren - zonder files.
Bron: Fraunhofer Presseinformation